Initiation aux principes du Lean Manufacturing
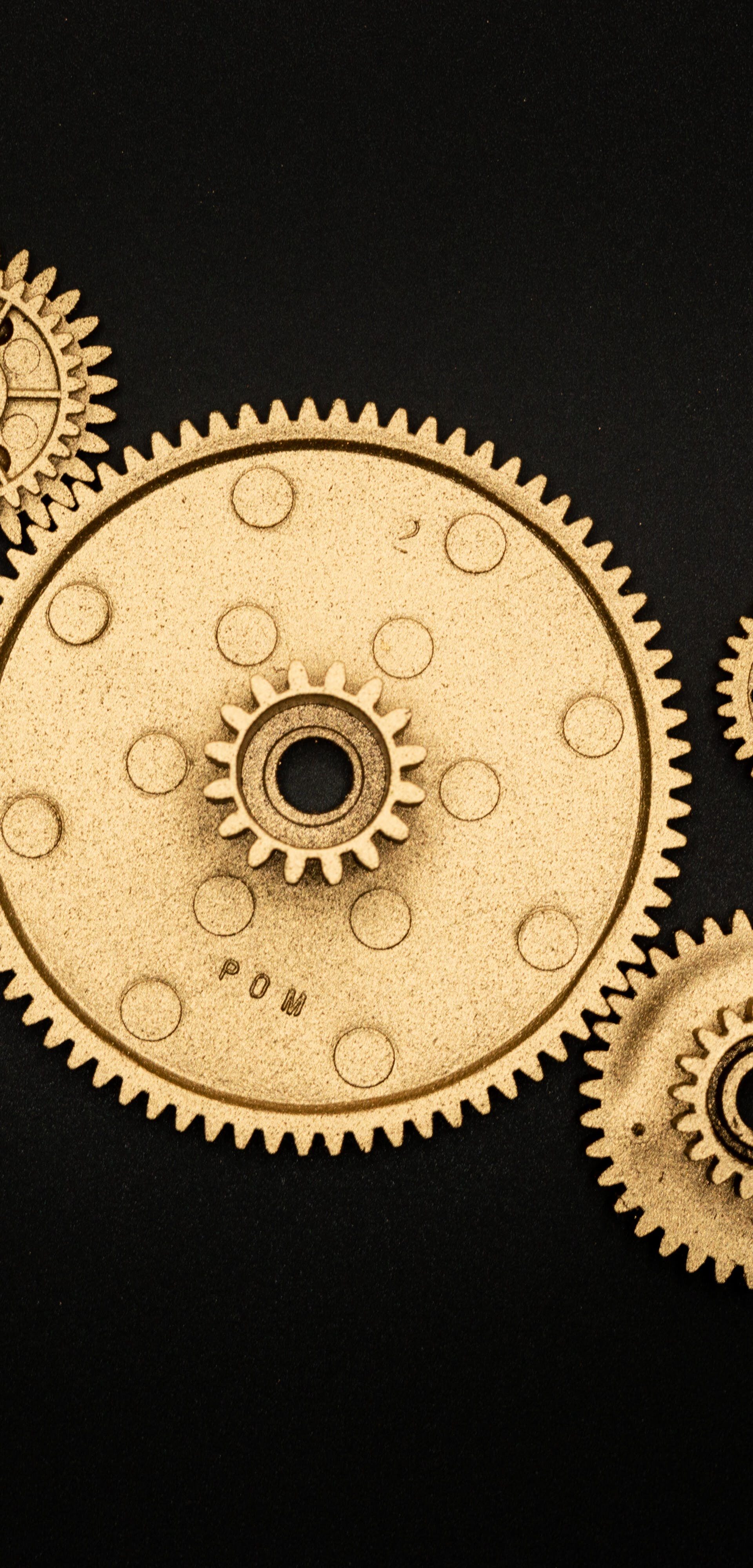
Avant-propos
Vous ne connaissez pas l’amélioration continue ?
Et pourtant, c’est une philosophie de « bon sens » à laquelle vous êtes confronté quotidiennement.
Par exemple, quand vous rangez votre garage, vous mettez spontanément ce dont vous avez le plus besoin, proche de vous, et ce qui ne sert que très rarement, au fond. Et bien ça, c’est de l’amélioration continue ! Alors c’est un peu caricatural, mais j’insiste : Le Lean management est une méthode de « bon sens », que tout le monde peut mettre en place. Bien sûr, son application est plus complexe dans l’industrie, mais il faut garder cette notion en tête.
Pour commencer, revenons sur les préjugés qui persistent en entreprise :
- « Amélioration continue », « Lean », « Lean management »… contribuent au licenciement des personnes.
FAUX. Les ressources sont utilisées différemment, et les collaborateurs sont formés, pour évoluer vers un poste moins répétitif, et plus gratifiant.
- « Le Lean ça ne sert à rien ».
FAUX. C’est souvent le « bon sens paysan » qui prime, à la portée de tous, et qui fait diminuer les coûts de production
- « Cela nous fait perdre du temps ».
FAUX. Prenons l’exemple de documents à compléter. C’est chronophage et semble parfois redondant MAIS cela va permettre de gagner du temps plus tard dans le processus. Il est important d’avoir une vision globale pour comprendre un projet. C’est pourquoi, il est essentiel de maintenir un bon niveau de formation et de communication sur les différents projets Lean.
Dans cet article, nous verrons les 3 points principaux du Lean Management :
- La valeur ajoutée
- Le gaspillage
- Les flux
Introduction générale au Lean Management
Le Lean Management est une méthode qui utilise de nombreux outils, afin de réduire les pertes, et d’utiliser le moins de ressources possibles.
Je qualifierai le Lean de philosophie de « bon sens » des personnes. S’il est parfois « facile » de voir les premiers problèmes du système de production, il est important d’approfondir en utilisant les outils qui sont mis à notre disposition.
Vous connaissez sûrement la loi de Pareto (aussi appelé le 80/20). Je trouve qu’il est intéressant d’adapter ce concept de la manière suivante : 20% des efforts représentent 80% des problèmes à résoudre. Un petit effort peut donc apporter beaucoup.
Le Lean Manufacturing se base, sur une méthode de l’amélioration continue : La roue de Deming (que l’on voit ci-contre), aussi appelé « PDCA ». Elle permet de s’améliorer, sans redescendre la pente.
Cette roue est remplie de 4 concepts :
- Plan : Préparer, planifier
- Do : Appliquer, mettre en œuvre
- Check : Contrôler, vérifier
- Act : Ajuster, corriger, réagir
La roue est également stoppée par une « Cale », qui empêche la roue de régresser, et cette cale est la représentation des « Audits », qui permettent de maintenir un bon niveau d’amélioration, et de ne pas redescendre.
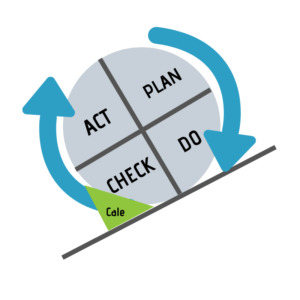
De plus, il est important d’avoir de bonnes bases avant de lancer des actions d’amélioration continue. Cette notion est représentée sous la forme d’un temple (exemple ci-contre : chez Saint Gobain). Pour atteindre l’excellence opérationnelle et la satisfaction du client (qui se trouvent en haut du temple), il y a différents piliers sur lesquels il faut travailler, comme la Qualité ou la Fiabilité.
Et les fondations sont très importantes, pour que le temple ne s’écroule pas. Ces fondations sont le 5S (une méthode d’amélioration de son environnement, qui seront traités dans un prochain article), l’implication du personnel,…etc.
Après cette courte présentation de l’amélioration continue, je vais développer quelques thèmes qui me semblent importants pour se lancer en amélioration continue. Cet article n’est pas exhaustif, puisqu’il existe une multitude d’approches, d’outils,…
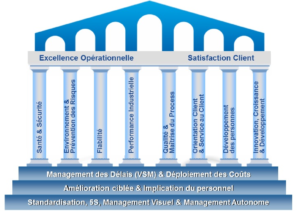
La valeur ajoutée
La valeur ajoutée, nommée VA, est l’ajout de richesse sur un produit, de l’entreprise. Cette valeur ajoutée exclue le gaspillage (dont je parlerai plus tard) et par conséquent, toutes les actions superflues, qui n’ajoutent pas de valeur au bien.
La valeur ajoutée peut s’exprimer ainsi :
- VA = Valeur finale du produit – Valeur des biens utilisés à la création (Bouami D., 2023, Le grand guide du Lean Management, Editions Afnor)
Pour approfondir, on peut calculer cette valeur ajoutée de 2 manières différentes :
- Grâce au résultat net
- Ou à partir de la marge commerciale (Bouami D., 2023, Le grand guide du Lean Management, Editions Afnor)
- Ces calculs vont aider à cibler les lieux où il y a des améliorations à rechercher (Bouami D., 2023, Le grand guide du Lean Management, Editions Afnor).
Le calcul de la VA est théorique et fastidieux, mais important pour définir les objectifs. Je vais maintenant présenter, ce que l’on appelle « les gaspillages », et comme nous venons de le voir, tout ce qui s’apparente à du superflu, qui n’ajoute pas de valeur au produit.
Les gaspillages
Dans le Lean Manufacturing, le superflu est défini par les 3M (en japonais).
Ces 3M signifient :
- Muda = Gaspillages
- Mura = Irrégularité du système de production
- Muri = Excès
Et dans les gaspillages, il y en 7 types de Mudas différents :
- Le stock et les encours de pièces
- La surproduction
- Les transports
- Les changements de série
- Les rebuts ou reprises après une erreur
- Les temps d’attente processus
- Les mouvements inutiles
Tous ces gaspillages, n’apportent pas de valeur ajoutée au produit, il est donc intéressant de les réduire au maximum, afin d’éviter de perdre de l’argent.
Le Lean Manufacturing propose des méthodes plus ou moins élaborées, pour identifier les pertes dans l’entreprise. Comme par exemple : le Kanban peut servir à diminuer la surproduction, les 5M (outil pour trouver la racine du problème, que j’expliquerai dans un futur article) mettent en évidence les attentes inutiles, mais aussi les cartes de contrôle pour vérifier que le processus est stable.
Je viens d’évoquer les gaspillages qui font perdre de l’argent à l’entreprise, et maintenant je vais parler du flux, qui est très important dans le Lean Manufacturing.
Flux
Tout d’abord, il est important de définir le flux : Le flux peut matérialiser le déplacement de la pièce dans les différents ateliers (usinage, sérigraphie, conditionnement,…), mais il peut être aussi le « déplacement » des documents, comme les ordres de fabrication (OF). Il est important d’étudier ces flux pour détecter les déplacements inutiles et ainsi cibler les actions à mener. En effet, il existe 3 flux : le flux de produits, le flux d’information et le flux humain.
Pour mettre en évidence les flux, il est important d’utiliser la VSM (Value Stream Map) qui est la cartographie des flux. Cette cartographie va permettre de cibler les postes d’amélioration. Elle va être aussi un point de départ pour communiquer avec les collaborateurs. Il existe de nombreuses codifications graphiques qui permettent de décrire l’entreprise (mais cela sera le sujet d’un prochain article dédié)
Voici un exemple de VSM en amélioration continue :
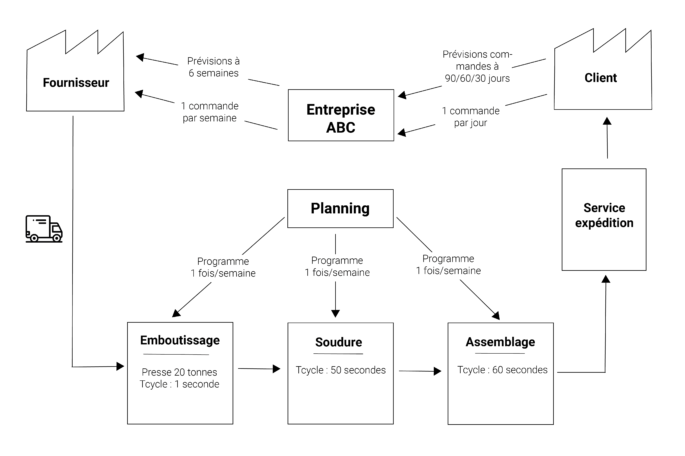
Sur cette cartographie, les flux sont schématisés par des flèches. Il faut bien connaitre le système de production, et notamment les temps de cycle (TC) ou le Lead Time (LT) qui est le temps entre la commande et la livraison.
D’autres part, il existe plusieurs types de flux :
- Flux continu = il vise à éliminer les gaspillages dans les chaines de production. C’est une suite d’activités qui permettent de réduire les périodes d’arrêts et d’attente. C’est ce flux vers lequel on tend, lorsque l’on fait du Lean.
- Flux poussé = La chaine de production produit, sans se soucier de la demande du client
- Flux tendu = L’entreprise achète des matières premières pour fabriquer le produit, une fois que le client a fait une commande (Demarque J., 2023, Shippr)
- Flux tiré = La commande du client « tire » la mise en production de produits (2020, Rubafilm)
Ainsi, vous avez pu découvrir les notions importantes du Lean Manufacturing. Le détail des outils spécifiques pourra faire le sujet de prochains articles. Il est important d’intégrer les concepts vus ci-dessus, avant de lancer des actions d’amélioration continue.
Finalement, pour éviter tout malentendu, je voudrais souligner que les premières améliorations peuvent être menées en production assez « facilement », avec un peu de bon sens, mais le management du projet doit ensuite être mené par un ingénieur en amélioration continue, pour effectuer des changements en profondeur (grâce à des outils plus complexes), et pour pérenniser le projet dans le temps.
M.Adeline
Bibliographie
- Cours d’amélioration continue, 2015, INSA CVL
- Maud Liron, 2022, Envol
- Temple de l’amélioration continue, Saint Gobain
- Bouami D., 2023, Le grand guide du Lean Management, Editions Afnor
- Maser Engineering, 2021
- Demarque J., 2023, Shippr
- 2020, Rubafilm